The Journey of a Breakthrough
After three-plus years of obsessive refinement, our first-of-its-kind avalanche airbag pack can finally be yours. Here, everything to know about LiTRIC.
“There’s snow in the mountains!”
I breathed a deep sigh of relief. Like most skiers, Anna Dixon, the manager of research and development at Arc’teryx, couldn’t contain her excitement about a high-altitude dusting in our backyard Coast Mountains. Together on a call to discuss a groundbreaking product, we were joined shortly after by Gord Rose, a senior industrial designer and another avid skier. But the palpable buzz wasn’t just for fresh snow during a frustratingly dry season. They were about to launch a project that had been three-plus years in the making: the LiTRIC avalanche airbag.
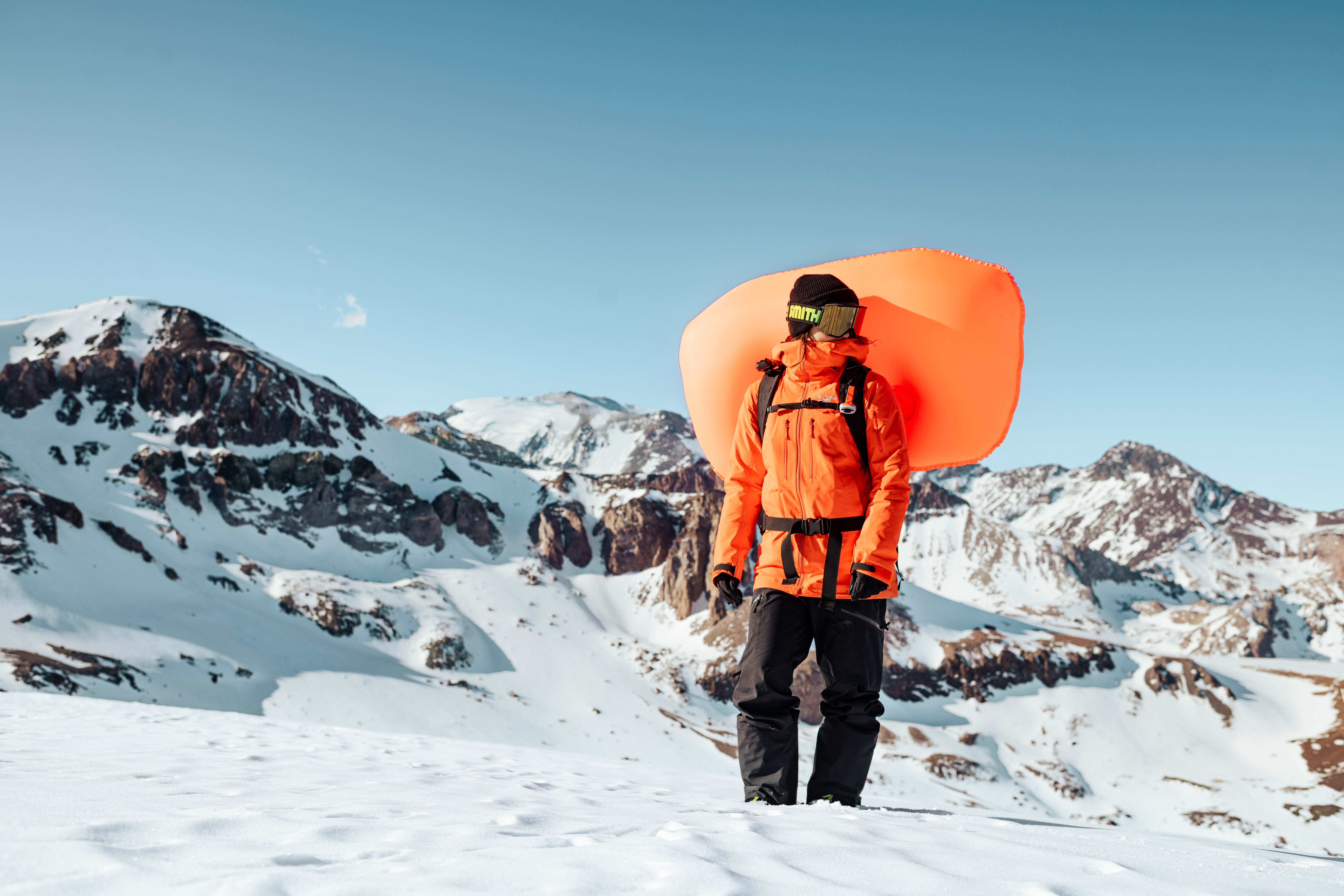
The Pack Probe
For skiers like Rose and Dixon, who played pivotal roles in bringing LiTRIC to life, avalanche airbag technology is nothing new. Developed in the early ’80s in Europe, the technology and popularity of these bags made their way to North America about a decade later, gaining popularity among the everyday skier and eventually booming in the late 2000s. As they gained global buy-in, skiers (and born problem solvers) like Rose and Dixon started to poke holes in the technology.
The packs relied on canisters of compressed air to fuel the inflation of the airbag, a large pouch folded inside the pack that, when filled with air, would keep skiers and snowboarders on the surface of the sliding snow in the event of an avalanche. While the concept worked, it had its flaws: The compressed gas canisters were heavy and not easy to travel with, and the bulky nature of the technology hampered overall pack design. While they were certainly an important life-saving device, for many skiers, the systems were restrictive.
But lucky for Rose, a junior designer at the time, Arc’teryx focused on innovation. Being a brand that specialized in packs, the team felt compelled to find a solution. After more than a decade of prototyping, a lightbulb went off: Instead of using compressed gas, why not use electronics?
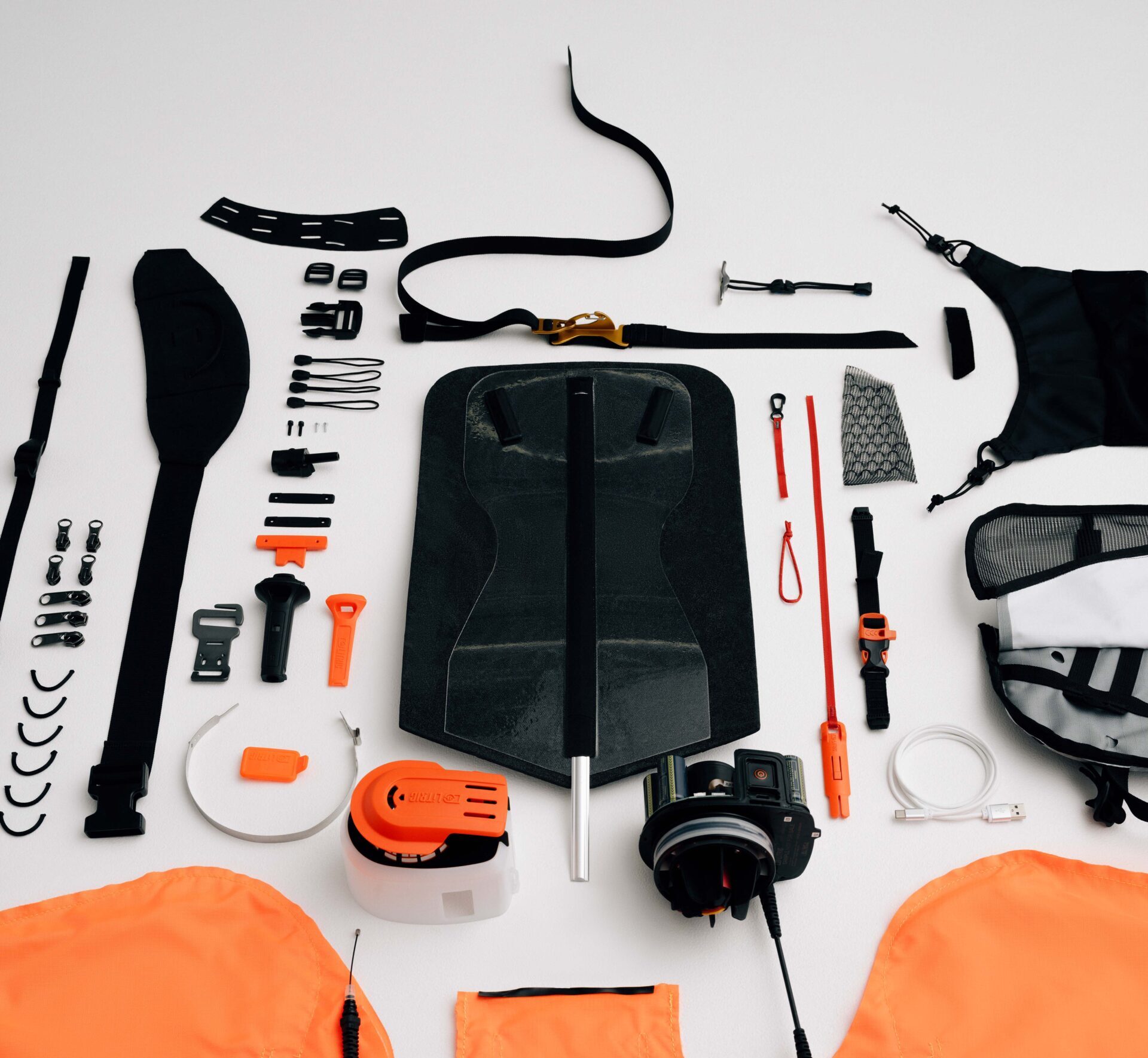
Getting Crafty
“For the first test, we literally went down to a hobby store, bought a ducted fan, and jammed it into an old prototype pack,” Rose recalls.
From there, the team kept exploring. Tom Fayle, the director of advanced research and development, happened to have young kids with toys that had lithium polymer batteries and DC motors. These became test pieces for the crew. There were mishaps, and even a few small explosions. But more important, there was a new energy.
“We were like holy sh*t; that was the paradigm shift,” says Rose. “From then on, I pretty much started working full-time on developing an electronic system, benchmarking it against all the work we had done with compressed air.” The result? The Arc’teryx Voltair.
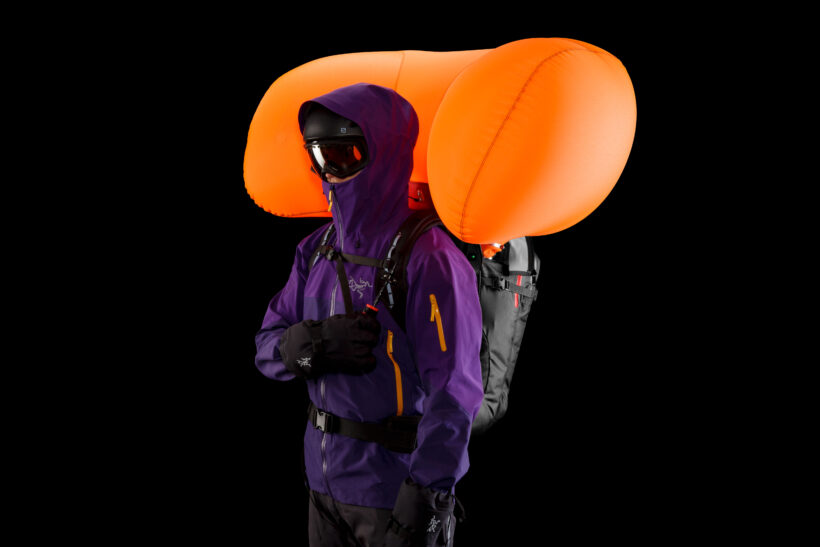
“We kept accumulating a list of things in the back of our minds that we wanted to improve,” says Rose. “That very long list gave us a really good starting point when Ortovox, our partner, approached us.”
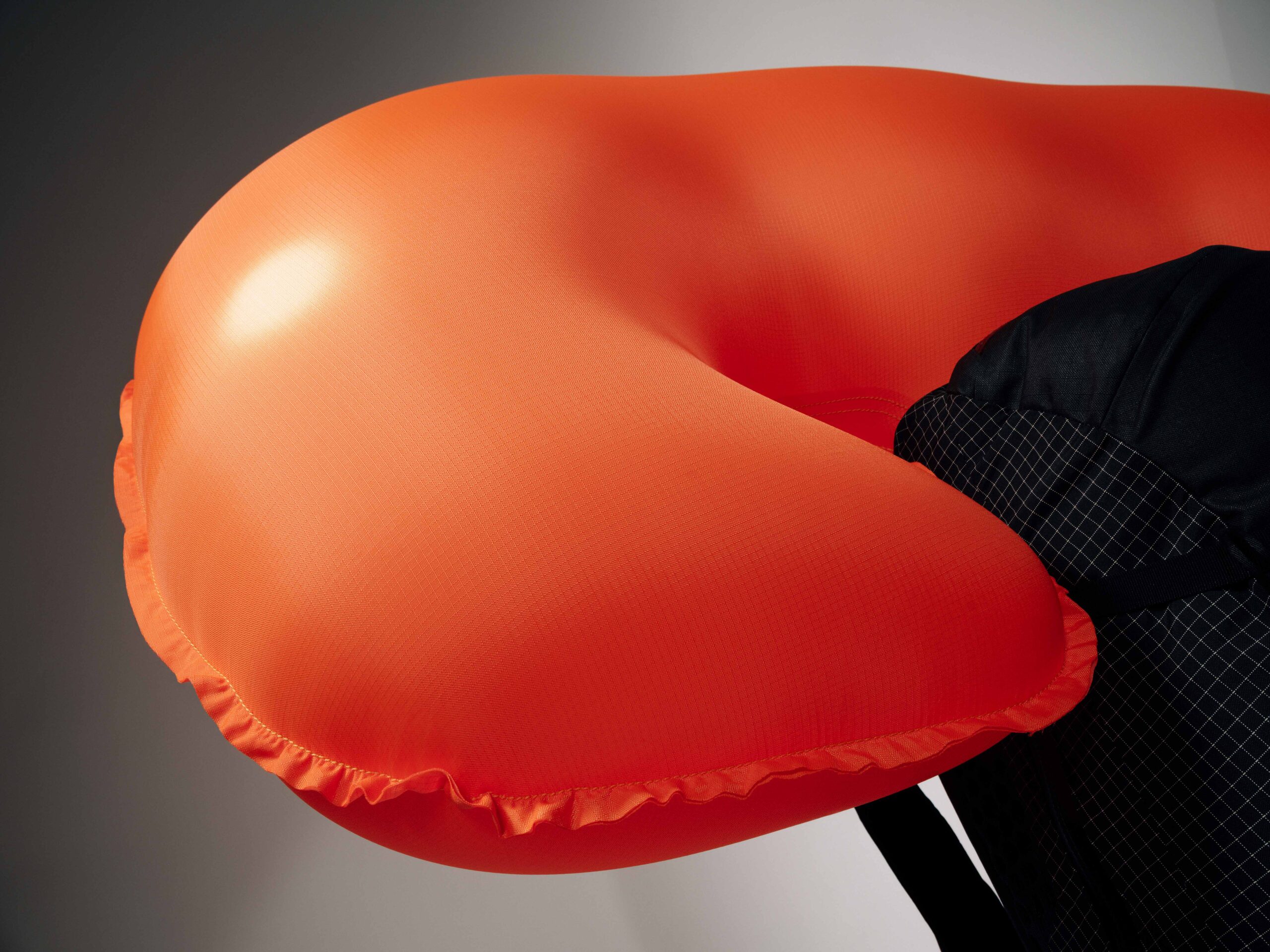
The Lure of LiTRIC
First on the list for a new prototype was keeping the charging system simple and adaptable. That meant two batteries that are USB-compatible and can be charged on an airplane. The next focus? Weight. The team was able to reduce the balloon weight by 25 percent, says Rose, as well as lighten the weight of the actual pack and its features. Beyond that, every design update revolved around keeping it a true ski pack — something light, yes, but also low-profile.
“We wanted to bridge the gap between our touring packs, with their super trim fits, and the LiTRIC series,” says Rose.
As if a game-changing design wasn’t enough, the team also had their eyes set on two other goals that are integral to any design process at Arc’teryx: repairability and durability. Rose understood the importance of having a pack that you can rely on year in and year out. With that in mind, the team built the pack with easy-to-repair zippers and interchangeable hip and shoulder straps.
Beyond countless laboratory tests on the battery, airbag, and trigger system, the pack has been tested by the team at Arc’teryx in the best testing grounds a skier could ask for: the powder-graced slopes of Vancouver’s North Shore mountains, minutes away from the Arc’teryx headquarters. And the testing grounds have paid off.
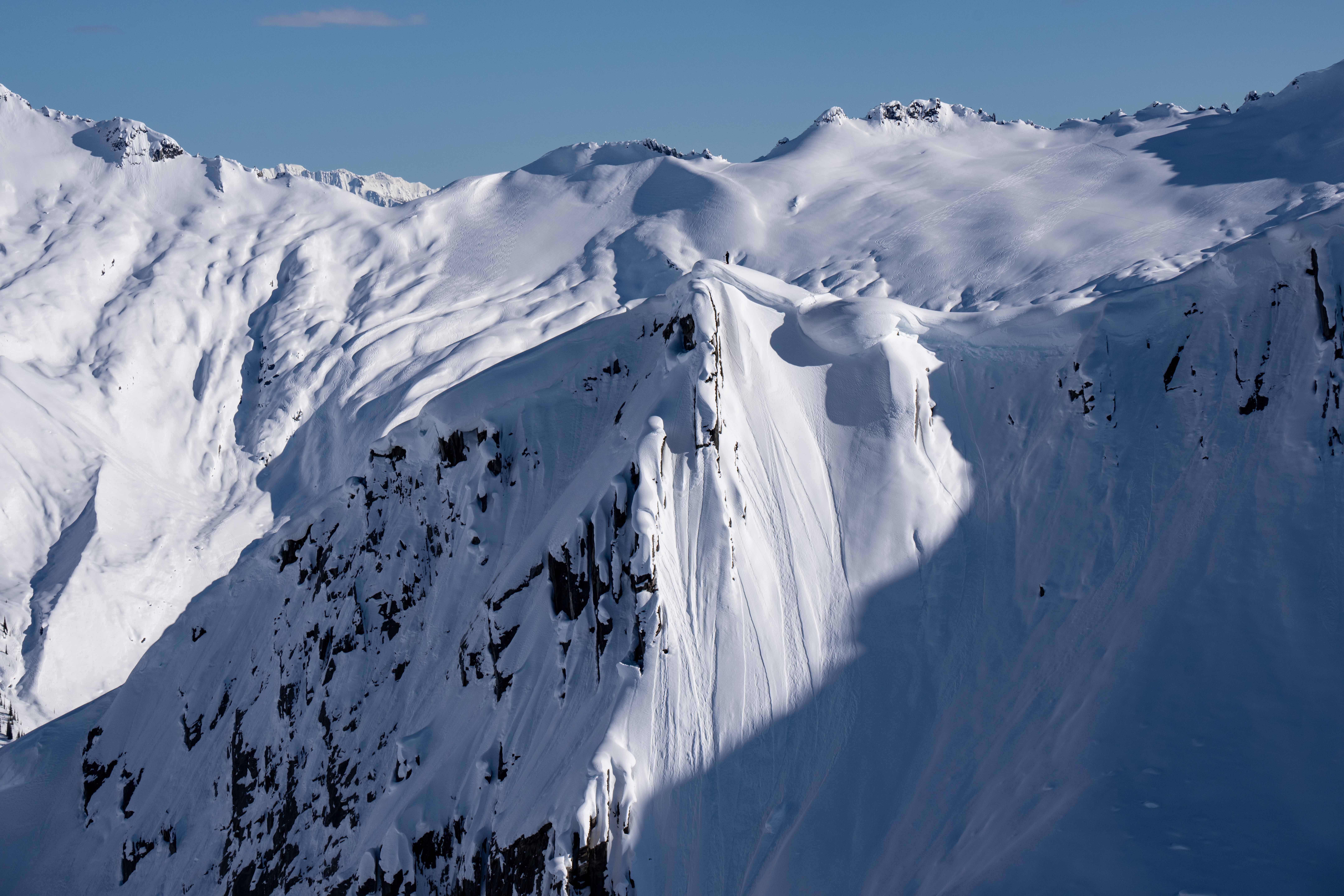
An Epic Evolution
Like few other avalanche bags, the fan system and airbag are neatly tucked into the top of the pack, offering plenty of gear storage for a day of ski touring. That means no having to sacrifice on other safety gear (or snacks) while wearing the pack. The slim, body-hugging profile also stays out of the way so that skiers and snowboarders can focus on pushing their limits in the backcountry.
The cherry on top? A stuff sack–inspired method to re-prep the system after a deployment, rather than fussing with folding.
All these nuances don’t come by chance. They come from care, not just experience, and a deep understanding of what makes a good pack.
“We’ve been testing every single part of this product since day one,” says Dixon. “You build prototypes, you evaluate them, you test them, you take them out again and again. So yeah, we’ve been skiing with this pack for some time.”
For Rose and Dixon, that process of going out into the field, critiquing each part of the pack, and going back to the drawing board is what drives them. In fact, it’s what started the long road that’s brought them to LiTRIC, and it’s what will bring them to the next iteration too.
Just like a skin track, the only place to go is onward and upward, one stitch at a time.
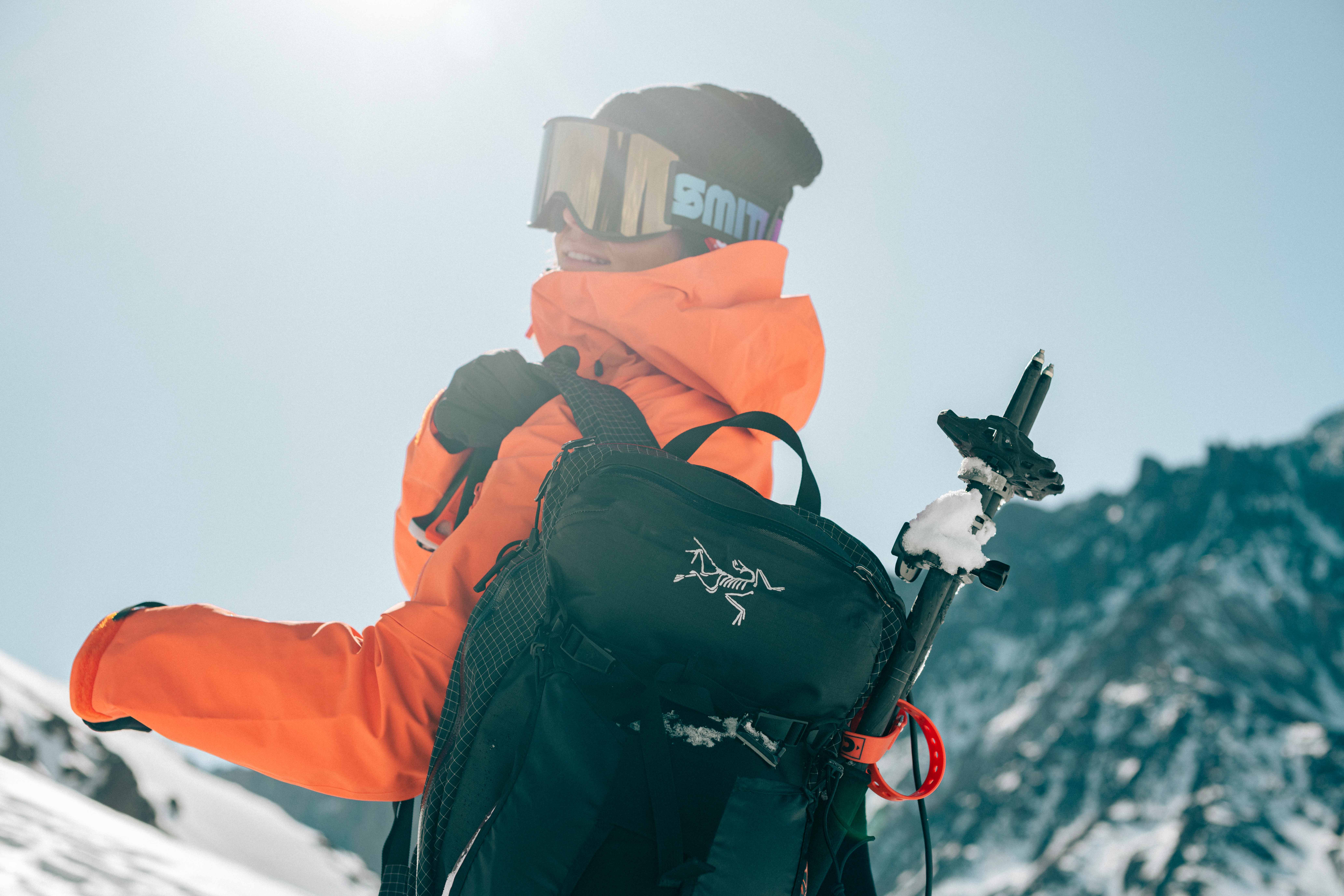